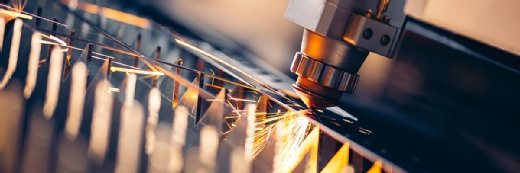
Parilov - stock.adobe.com
How BE Switchcraft is using RFID to streamline manufacturing
The Australian switchboard manufacturer has rolled out a radio frequency identification system to track production jobs and streamline manufacturing processes
Having visibility over the factory floor is crucial for any manufacturer ensure production efficiency and to meet production deadlines. To Australia’s BE Switchcraft, which makes customised electrical switchboards that distributes power in buildings, that visibility was not available until recently.
Based in Adelaide, South Australia, BE Switchcraft had relied on manual processes and paper-based spreadsheets to document the production status of each switchboard, which passes through six different areas within its factory.
The processes and spreadsheets were not just cumbersome, the company’s production crew also found themselves dealing with outdated and legacy data, making it difficult to track where each switchboard was in its production lifecycle.
To address the issue, BE Switchcraft implemented a barcode-based system where factory workers overseeing different production stages would scan barcodes printed on the documentation of each switchboard to record the status of a job.
But in a manufacturing environment where machine operators don gloves, it was hard for them to pick up a barcode scanner and record the data. Consequently, the barcode-based system did not receive buy-in from the production crew, said Anthony Spadavecchia, managing director of BE Switchcraft.
The company went around looking for alternative solutions, eventually settling on a radio frequency identification (RFID)-based system with hardware supplied by Zebra Technologies.
“We wanted a zero-interaction technology,” Spadavecchia said. “I didn’t want any of my guys to have downtime and it has to be seamless – RFID seemed to be a logical move even though it isn’t a mainstream technology in manufacturing.”
Instead of using barcodes, the company attached RFID tags to the documentation that follows each switchboard being made. As the switchboard passes through different areas in the factory where processes such as metal folding, punching and welding are carried out, an RFID reader automatically scans the tags to record the status of a job.
“We can now track our jobs in real time and upload the data daily to our ERP [enterprise resource planning] system,” Spadavecchia said, adding that managers can now tell where the switchboards are in the production lifecycle via a dashboard and assign more labour to work in areas with production bottlenecks.
The entire system, including the dashboard, was implemented by BE Switchcraft’s in-house technology team. Spadavecchia said some of the work involved converting the hexadecimal data picked up by the RFID scanners into logical data that corresponds to different locations in the factory.
However, the zero-interaction nature of the RFID system created doubt among the company’s production crew.
“They thought the system wasn’t going to be robust, purely for the fact that there was no interaction,” Spadavecchia said. “You virtually walk past the scanner with one of these [RFID tags] and it works – they struggled to get their heads around that.”
Spadavecchia said over time, the production crew eventually trusted the system to do its job as they began to rely more on the data that was being captured.
There were some technical challenges as well. In one area of the factory, the high motor load of some machines created RF interference that corrupted the hexadecimal data captured by RFID readers.
“We had to tune the frequency of the readers, and in some areas, we had to relocate the readers one or two meters away,” Spadavecchia said.
Spadavecchia said the RFID system has reduced labour by 10% as the production crew no longer needs to spend time tracking down jobs on the factory floor.
“We were wasting many hours of labour trying to find the jobs and whether we had ordered all the raw material and had the right labour in the right spots,” he said. “We’ve smoothed that out and now we can see gaps in our manufacturing process easily.”
In future, the company hopes to go beyond dashboard reporting and use the data to communicate directly with machinery.
“That would be the next version of our automation where we can integrate our CNC turret punches and brake presses with the data and preload the SolidWorks files into the machines by batches,” Spadavecchia said. “We’re still a little way off, but that will save the operator from manually loading the files into the machines.”
Read more about IT in Australia
- Tata Consultancy Services worked with the Australian Energy Market Operator to build a new system that speeds up electricity market settlement.
- Telstra will use Azure as a preferred cloud while Microsoft will look at boosting its capacity on Telstra’s subsea cable network in a wide-ranging deal.
- The AskVic WhatsApp chatbot will provide culturally and linguistically diverse communities in Australia’s state of Victoria, with Covid-19 information and support.
- With a strong DevOps culture, Bendigo & Adelaide Bank has been moving its most important applications to the cloud in a journey that has already reaped returns.