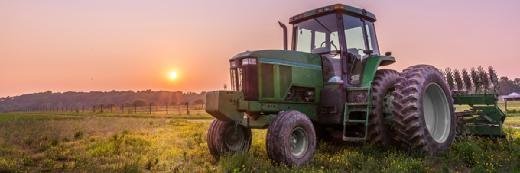
flownaksala - Fotolia
CW Innovation Awards: Sime Darby ups ante in service management
Sime Darby Industrial’s inService Suite has returned more than 100,000 hours to the company in a digitisation initiative that has improved efficiency and customer engagement
The industry is replete with stories of how enterprises embark on Digital transformation projects but fail to achieve the desired results.
Knowing this, Sime Darby Industrial was determined to avoid falling into what the machinery-based giant terms as being merely “decorative digital” – where money is invested into digital systems that nobody uses.
To avoid this pitfall, the company’s top management created a clear alignment between the chief technical sponsor and business owner for a digitisation project as part of its group-wide Service of the Future transformation.
The aim of the project was to develop a software platform aimed at increasing its efficiency and engagement with customers across the five countries in which it operates in Asia.
Using a top-down approach, both technical and business sponsors drove the direction of the project and became the face of the company’s digitisation initiative.
“The project was successful because we tried new ways of working,” said Teodoro Stechmann, executive manager for technology solutions and strategy at Sime Darby Industrial.
“We practised a ‘think big, start small and scale fast’ mentality and this created innovative digital solutions that delivered value to our businesses.”
Achieving innovation
Known as the inService Suite, the key functions of the platform – which helped Sime Darby Industrial clinch the manufacturing category in the Computer Weekly Innovation Awards APAC – included centralised scheduling, integrated communications, work order management, field automation for mobile technicians, and automated timesheet processes.
The company needed to seamlessly integrate those functions to its existing Microsoft Dynamics ERP (enterprise resource planning) system using robotic process automation (RPA). This eliminated the need for manual job assignments and allowed labour to be repurposed for higher-value jobs. It also reduced data entry errors.
At the same time, the company employed the internet of things (IoT) and Google Maps to capture vehicle telematics and help it schedule work efficiently. Complementing this was the use of speech-to-text and artificial intelligence (AI) to enhance the user experience.
Overall, the company claimed that project milestones were delivered faster than expected, while the cost of the project was less than A$500,000 to deliver the minimum viable product (MVP).
In quantifying the benefits of inService Suite, Sime Darby Industrial said its use of RPA saw more than 490,000 timesheets fully automated, returning over 100,000 hours to the company. Timesheets were also submitted by technicians within 24 hours at the end of their shifts.
The company also increased its net loyalty scores (NLS) from 21% to 56% within five months, while supervisors had greater visibility of its resources, improving the efficiency of its technicians by 8%.
Managing change
In building the platform, the project team relied on the agile methodology to re-engineer business processes and implement changes without having to reiterate later.
During the “ideate” stage, the team observed the day-to-day life of users through weekly webinars and encouraged early adopters to use the product, so it could receive immediate feedback.
When deploying production systems, the company designed a change and communication plan to help the team understand what was happening on the ground.
Recognising the complexity of the deployment, which involved five countries and multiple branches, the team developed self-service multimedia articles and FAQs within the inService Suite itself so that users could educate themselves.
The next level of support was achieved through an omnichannel support service with AI capabilities, which greatly reduced the number of employees required to support more than 8,000 users across the region.
With all that in place, Sime Darby Industrial managed to deliver this digital initiative to more than 6,000 employees and hundreds of customers, with scalability in mind to ensure that it could be cost-effective and be easily replicated across the Sime Darby group.
“For us to succeed, we needed a culture that has the ability to move and be agile and to support our staff to see themselves as digital workers,” said Dean Mehmet, managing director for Hastings Deering, a subsidiary of Sime Darby Industrial. “It’s not about seeing digital as a threat, but as an enabler for them to have a greater experience coming to work.”