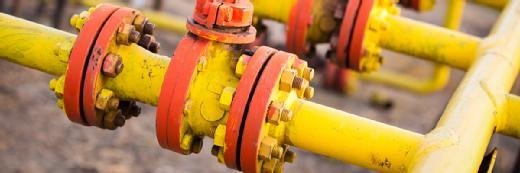
zorandim75 - Fotolia
CW Innovation Awards: Bharat Petroleum refines operations with a digital nerve centre
Bharat Petroleum has developed a digital nerve centre powered by the internet of things and artificial intelligence technologies to monitor the journey of its products
Running a large ecosystem that encompasses refineries, plants and thousands of retail outlets, Bharat Petroleum Corporation Limited (BPCL) knows that any oversight in its vast operations can affect the quality of its services and customer satisfaction.
To ensure it stays on top of things, the Indian organisation has adopted key technologies such as artificial intelligence (AI) and the internet of things (IoT) to manage its expansive ecosystem.
Owned by India’s Ministry of Petroleum and Natural Gas, BPCL is headquartered in Mumbai, where it operates a refinery, and has a second site in Kochi. The Fortune 500 company manages a network that includes 17,000 retail outlets across the country, 75 terminals, 54 liquefied petroleum gas (LPG) plants, and more than 25,000 tankers.
It values the need to build trust and assure customers that it is able to maintain quality, quantity and price of its products at any point in time. It does so by embracing digital technologies and transformation initiatives under the government’s Project Anubhav programme.
An important piece of this is IRIS, Bharat’s digital nerve centre, which has been designed to monitor the entire journey of every product – spanning fuel terminals, LPG plants, and customers’ own premises – delivered to its clientele. The integration of these on a single platform provides a single view of the company’s entire value chain.
The main goal here was to ensure that any potential hiccups along the way can be quickly identified and addressed, safeguarding the BPCL brand, which is associated with premium service quality.
Powered by AI and machine learning capabilities, the digital nerve centre can accept more than three million inputs a second from local automated systems, cameras and other IoT devices deployed at various locations. These include retail outlets, LPG plants, fuel terminals, consumer pumps, railway installations and delivery tank trucks.
IRIS, which helped BPCL to clinch the public sector category in the Computer Weekly Innovation Awards APAC, can track performance according to key parameters that help deliver faster fuelling with higher safety, among other benefits. This also establishes compliance across BPCL’s supply chain and monitors equipment health to ensure critical systems remain up and running.
And when issues arise, alerts are automatically triggered, prompting the necessary actions to be taken, including rapid response for equipment failures or hazardous incidents. This constant monitoring also enables the company’s employees across India to make more accurate decisions and take pre-emptive steps swiftly to resolve issues that, if left unresolved, can harm service quality.
Appropriate follow-up actions are established based on predefined thresholds and a workflow management system pushes alerts and escalates unresolved issues based on preset workflows.
For instance, reminders for preventive maintenance events can be established according to a predetermined frequency, such as scheduled tests of earth pits and fire extinguishers at depots and LPG plants.
Armed further with AI and machine learning technologies, BPCL can access valuable data insights to continuously fine-tune its operations for greater efficiencies, security and safety. This can go a long way to deliver quality service experience to more than 10 million BPCL retail and commercial customers.
Located in Noida, the digital nerve centre provides a host of business benefits, including:
- Cost savings from preventive maintenance.
- Better support for field officers to service customers and suppliers.
- Reducing loss of sales with automated stock monitoring.
- Compliance with service-level agreements.
- Identifying HSSE (health, safety, security and environment) violations through video analytics.
- Enhanced safety and quality checks at plants to reduce defective cylinders.
Also, the use of bidirectional communication between controllers and other systems deployed at operating sites enables equipment to be shut down promptly when there are violations of standard operating procedures (SOPs).
Key timelines
Major projects such as IRIS, which is hosted on BPCL’s private cloud, can suffer delays and missteps, so BPCL took care to break the deployment into several key milestones, each with a specified timeline for completion.
It also set up a project team of business users to establish use cases and SOPs, as well as monitor its progress daily.
Also, suppliers and vendors involved in the deployment of automation systems, video analytics, vehicle tracking system, firewall and overall IT infrastructure were brought into the fold to ensure their individual projects were completed on time.
All stakeholders were kept updated through presentations and training decks, infographics, and regular email communication. Selected teams also were invited to Noida to visit the digital nerve centre, enabling them to experience IRIS first-hand and learn more about its features and benefits.
BPCL viewed this as especially important because the success of any technology adoption depended on empowering its employees to create a safe and efficient environment encompassing operations, logistics and service delivery.
The project is set on a 12-month timeline, although the government entity expects to complete it within eight months and with a budget of 25 crores (US$3.4m).
Read about other CW Innovation Awards winners
- A blockchain-based system developed by Singapore-based Zuellig Pharma can help governments and healthcare providers weed out fake vaccines and manage vaccine distribution and administration.
- Sime Darby Industrial’s inService Suite has returned over 100,000 hours to the company in a digitisation initiative that has improved efficiency and customer engagement.
- Singapore Airlines has expanded its blockchain-based digital wallet into a broader digital lifestyle platform.
- Flybuys, Australia’s biggest loyalty platform, takes 12-month journey towards the cloud, slashing time to deliver customised offers to less than 45 minutes, among other outcomes.