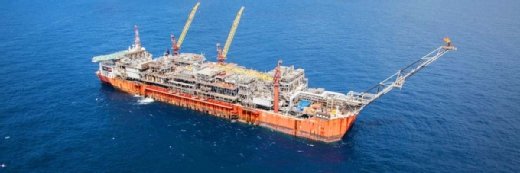
Giles Barnard
How Shell is fleshing out a digital-twin strategy
Digital twins are among the innovations that use AI, IoT and big data to help asset-intensive industries manage their operations
Shell is among the growing number of companies that are pioneering digital-twin technologies, and recently signed a deal with Aveva to implement an engineering data warehouse to support digital twins in asset lifecycle management.
The oil and gas company has several digital-twin initiatives to support its operations. The coronavirus crisis has made the use of such simulation technology more important, because a digital twin can help to minimise the number of staff required at a facility for on-site maintenance. Thanks to artificial intelligence (AI), a digital twin can also improve safety and reduce operational costs through predictive maintenance.
Analyst Gartner has forecast that by 2023, one-third of mid- to large-size companies that implement IoT (internet of things) will have deployed at least one digital twin associated with a Covid-19-motivated use case. Used in an industrial context, IoT enables machines fitted with sensors to collect data about their wellbeing and environmental conditions.
Not only can local processing at the edge enable these devices to use this data to deal with situations in real time, but the data can also be collated centrally and fed into digital-twin simulations. Becausee the model encompasses real sensor data from the machine being simulated, the digital twin enables engineers to understand how well the machine is operating and whether components need replacing.
Benoit Lheureux, research vice-president at Gartner, said: “Digital twins can help companies recognise equipment failures before they stall production, allowing repairs to be made early or at less cost.”
Lheureux said a company can use digital twins to automatically schedule the repair of multiple pieces of equipment in a manner that minimises the impact on operations.
Building resilient operations
In a transcript of the company’s second-quarter 2020 earnings call posted on Seeking Alpha, Shell CEO Ben van Beurden described how the company had accelerated digitisation initiatives during the coronavirus crisis. Among the areas of focus is a reduction of the company’s contingent workforce by accelerating automation and digitisation.
Van Beurden said: “We further integrated machine learning into predictive maintenance activities of our refining and our deepwater assets with the potential to now roll it out across other parts of the portfolio as well. We have implemented new digital features that allow us to further optimise the inventory of materials in our refineries, and we are increasing the use of artificial intelligence to run and optimise our assets in this unprecedented environment, as well as to simulate return-to-office scenarios for it.
“For us, all these actions are more than initiatives to just ensure business continuity through the crisis. They are actually opportunities to further build resilient operating models and optimise costs.”
Shell’s Bonga Main floating production storage and offloading (FPSO) vessel (pictured above), located 120km southwest of the Niger Delta in Nigeria, became operational in 2004. It has a capacity of 225,000 barrels a day and weighs more than 300,000 tonnes. It is using a digital twin developed by Akselos.
The model is regularly updated with loading conditions and inspection data, providing the ability to carry out structural assessments based on the “as is” condition, from anywhere and at any time.
Read more about digital twins
- The Power Systems unit of Rolls-Royce has begun using technology from Iotics to collect data points for engines in the field and build digital simulation models.
- Ingesting and analysing data from IoT sensors, digital twins can help organisations answer their most pressing business questions. Deloitte BV’s Helena Lisachuk offers the lowdown on digital twins.
Shell’s deepwater company in Nigeria and operator of the 225,000 oil barrel capacity plans to use the digital twin model to: identify critical areas for prioritised inspection, maintenance and repair; reduce the personnel on board the asset; reduce the necessity for physical inspections in hard-to-reach areas, such as cargo tanks; and support scenario planning for extreme weather events and asset modification.
According to Shell, the deployment of the simulation technology will also enable safe asset life extension by replacing the over-conservative estimates made with conventional simulation software, with accurate assessments that reflect actual remaining fatigue life.
Elohor Aiboni, asset manager for Bonga, said: “The Bonga Main FPSO heralded a number of innovative ‘firsts’ when it was built back in 2004, so it’s fitting that it is the first asset of its kind to deploy something as advanced as a structural digital twin. We are very excited about the new capabilities that Akselos brings and believe it will create a positive impact on the way we manage structural integrity. It is also a great example of digitisation coming to life.”
In a recent blog post, Victor Voulgaropoulos, industry analyst at Verdantix wrote: “Shell is again in the spotlight, as it seeks to further accelerate its digital transformation initiatives by implementing digital-twin solutions across its global portfolio of assets and capital projects. Shell has signed an enterprise framework agreement with Kongsberg Digital, a Kongsberg subsidiary, for the deployment of Kongsberg’s Kognitwin Energy, a cloud-based software-as-a-service digital-twin solution, within Shell’s upstream, liquified natural gas, and downstream business lines.”
According to Voulgaropoulos, Kognitwin Energy uses high-fidelity, physics-based models and machine-learning algorithms to simulate the actual operation of a plant or asset, and generates synthetic data where measurements are not available.
Simulating projects
Meanwhile, Shell’s Deepwater business has selected Bentley’s digital-twin approach to streamline its capital projects. With a plan to deliver several subsea tie-back projects over the next 10 years, the company is implementing an integrated digital project and engineering environment, which spans project conception in the early phase design through to handover.
“Shell Deepwater Projects is developing an integrated workflow and data platform from system selection to asset handover to streamline our capital projects processes and accelerate time to first oil,” said GT Ju, general manager, Gulf of Mexico Deepwater Projects.
“The platform is being developed in partnership with Bentley, leveraging Bentley’s iTwin open, scalable [Microsoft] Azure cloud-based platform, which provides interoperability across owner and supply chain systems. We believe that an end-to-end platform that gives us visibility and transparency to project and engineering data across our portfolio will be a key driver to delivering competitive projects.”