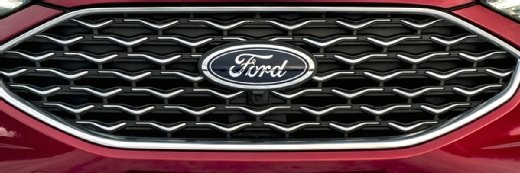
Ford
Executive interview: Ford’s Graham Hoare on manufacturing ventilators
The executive director for business transformation at Ford of Britain discusses how augmented reality supported the VentilatorChallengeUK effort
When the UK went into lockdown, prime minister Boris Johnson called on industry to help build ventilators for the NHS. Ford, McLaren, Airbus and Siemens, among others, were asked to contribute to the VentilatorChallengeUK effort.
Graham Hoare, executive director for business transformation at Ford of Britain, was part of a consortium, which included representatives from Airbus and Formula One team McLaren Racing, to scale up a ventilator design from Penlon.
Recalling the start of the project, he says: “The consortium formed shortly after the ventilator challenge call to arms on 17 March.”
Although it was the companies that made the news headlines, the consortium actually comprised a group of individuals from different companies. Penlon, based in Oxfordshire, originally developed a chloroform vaporiser, called ESO, for airborne forces during the Second World War. According to Hoare, Penlon had the ability to produce 50 ventilators a week.
“We developed ESO 2 for the pandemic,” he says. “From a standing start, we were producing 400 a day – equivalent to 25 years of Penlon’s ventilator production.”
The challenge involved working out how to scale up to 200 times the volume of manufacturing within six to eight weeks. “The only way we could envisage this scale was to leverage the capabilities of huge companies,” says Hoare. “We needed Siemens, Airbus and the Ford factories in Dagenham, and needed to bring together unique skills that were not next door to each other.”
With the government announcing strict measures to control the spread of the Covid-19 coronavirus, the initial stages of the project had to be organised and run by senior staff from the consortium’s 33 principle companies without them ever meeting in person.
“Competence for this ventilator was in the heads of a handful of people, some of whom were isolating,” says Hoare. “We really needed a way to get their insight and multiply that across the country.”
Technology played a critical role in linking the experts and the factories to operationalise the production of the ventilators. “No one had built a ventilator before; many had never seen one. Microsoft HoloLens has allowed us to reach across hundreds miles and build bonds across technology communities,” he says.
Visualising scale-up manufacturing
Hoare says augmented reality (AR) using HoloLens allowed the ventilator experts to “see” the factory floor and solve problems in real time.
“HoloLens has enabled this project to be successful. I would say that without it, we would not have achieved the objectives that we’ve achieved,” he says. “For our team in Dagenham, HoloLens became this direct bridge to Penlon in Oxfordshire. It changed a situation from one that was extremely complicated to envisage, to one that was far more tangible and reachable.”
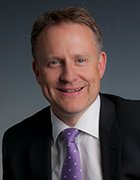
“No one had built a ventilator before; many had never seen one. Microsoft HoloLens has allowed us to reach across hundreds miles and build bonds across technology communities. It has enabled this project to be successful. Without it, we would not have achieved the objectives that we’ve achieved”
Graham Hoare, Ford
The use of HoloLens and Microsoft Teams has streamlined the problem-solving process. HoloLens was used to plan factory layouts at Dagenham and Airbus, diagnose problems remotely, train employees and for optimisation. Prior to using HoloLens, Hoare admits that the team struggled to describe problems they were encountering, and describes the process as “so redacted”.
For Hoare, the VentilatorChallengeUK demonstrates the viability of using remote communications and augmented reality in collaborative manufacturing projects. “We planned a £120m programme using Microsoft Teams. Many of us did not meet until four to six weeks into the project,” he says.
On-site meetings were only needed as and when it was necessary for the experts to obtain the level of technical detail that they could only get by being present and seeing the job. “The programme demonstrated the value of how we can extract competence from a medical device company and translate this to a car company,” he says.
HoloLens created a portal to support technicians at a nuts and bolts level.
Read more about augmented reality
- Augmented reality, virtual reality and mixed reality are becoming valuable tools in manufacturing, but it’s easy to get them confused. Learn about their similarities and differences.
- Etsi, the industry specification group on augmented reality, develops specification to enable multi-supplier ecosystem for industry and consumers.
Hoare says Microsoft Teams also became an important enabler for the project. “We created tens of thousands of documents. Just to get the CE mark we had to get 180 documents synchronised.”
He says Teams provides a way to democratise data, such that any team member can access the data they require. “We made data ubiquitous,” he says. “In some ways, it was easier to make data decisions than other decisions.” Teams was used for file transfers and for key meetings.
Remote problem solving
By using augmented reality with HoloLens, Hoare says the VentilatorChallengeUK team could replicate a problem in two locations. If a medical device created a very unique error condition, for example, the specialist could run a second machine in parallel with the team in Dagenham to recreate the failure situation.
The VentilatorChallengeUK project demonstrated remote collaboration across different companies. Describing his experience of video conferencing for collaboration, Hoare says: “Over half the team I hadn’t met before. Our entire relationship was online. It is not the same as the body language you read when in face-to-face meetings, being able to see someone’s face and understand their mannerism is effective. It is like a first date. That’s how it was...very effective.”
Hoare says he was surprised how quickly people adapted to working with the new technology, with a few key users adding significant value to the project just a few hours after first wearing HoloLens. “It is amazing when you have an ambition and you rise to the challenge. People are really adaptable and the tech is remarkably intuitive,” he says. “We haven’t scratched the surface of what we can do with the tech.”
The ability to use AR technology to accelerate innovation has set minds racing in Ford’s core business. As an example, a prototype vehicle can cost anywhere between $300,000 and $500,000 to build, and it may only last during the testing phase. Hoare believes there is an opportunity for augmented reality in prototyping, where engineers can design products using wearables like HoloLens.
“We would be able to look at the challenge of the build process and optimise the value of the prototype,” he says. “Faster prototypes mean faster time to discover problems.”
Ford is in discussions with the government on producing zero-emissions vehicles by 2030. Hoare says the VentilatorChallengeUK project has demonstrated the ability to transition to an efficient carbon footprint using connectivity across businesses.
Hoare says he has been involved in many exciting projects during his career, but describes this one in particular as “quite remarkable and inspiring”.