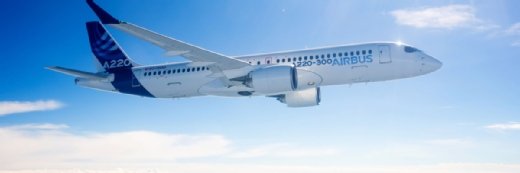
How Airbus handles IoT network traffic in manufacturing
The internet of things is set to power the fourth industrial revolution, providing data to optimise manufacturing. Airbus is starting to put sensors in aircraft assembly
Airbus is using internet of things (IoT) technology from HPE to support its assembly of aircraft.
During manufacturing, thousands of rivets are used to attach panels to an airframe, and the panels need to be drilled and fastened in a very particular way. Riveting must be done in the right order and the correct torque settings used for torque wrenches.
Airbus has estimated that it drills 120 million holes a year for fastening aircraft panels, and only 25% of this activity is automated. That means 75% of the work has to be done by human operators.
The assembly process involves drilling, riveting and then applying sealant to prevent corrosion. Sébastien Boria, mechatronics and robotics technology leader at Airbus, says: “These are the most critical activities in assembly. At the end of the day, humans are not predictable. They take a decision that will have an impact further down the production line.”
The manual processes for drilling and fastening panels requires tools to be configured with very specific settings, and panels must be fastened to the airframe in a consistent way.
If a tool operator works at a station on the aircraft production line for an eight-hour shift, but the panel being fastened takes 12 hours to finish, the work needs to be passed on to another operator.
Boria says there is a potential problem at the hand-over interface between the end of the first operator’s shift and what is then communicated to the next operator, who has to carry on where the first operator left off.
If the second operator then takes over, but works in the wrong way and the work needs to be redone, this could prove very expensive, says Boria. The answer is to monitor the work each operator does in near real time, so that production errors can be corrected immediately.
Latency can stop production
Today, the tools used by operators working on an aircraft’s construction have sensors. Typically, IoT applications deploy sensors at the so-called edge, onto physical devices, which then feed data back to a centralised control and feedback system, which acts like a supervisor.
Boria says: “If you consider network communications, your IoT application may work in a proof of concept, but then you need to scale on the factory floor.” This is where problems are discovered, he says.
“If you have infinite bandwidth, then you can have thin clients and a strong back-end,” says Boria. “But real life on the factory floor is clearly different from theory. You cannot stop production due to network disconnection or an issue with Active Directory. We need to avoid these issues.”
Read more about edge computing
- SDN and edge computing can work together to apply data-processing decisions that make better use of network links and bandwidth, especially when it comes to edge versus cloud.
- As IoT devices proliferate, cloud just isn’t fast enough. But that is exactly where edge computing comes in, enabling analysis at speeds the future demands.
The IoT application in a centralised architecture assumes it will always have a network connection. It depends on a reliable network supporting hundreds of operators using tools with sensors, all operating at the same radio frequency. The tools will all be sending data to the back-end system simultaneously, and this is likely to cause a network contention issue at some point, says Boria.
He thinks developers should consider network communications as a scarce resource. “If you assume you will have 5G and high bandwidth, then your applications will have problems with latency,” he says.
It takes a finite amount of time to send data over the network to the back-end system, leading to potential problems when data is lost or arrives late, says Boria. The typical way to overcome latency problems is to add more bandwidth, he adds.
Working at the edge
But Airbus realised that such an architecture would not be practical on the factory floor. “We do not need strong [network ] communications – we need strong things,” says Boria.
Instead of relying on a back-end server that knows everything about the process, with dumb clients at the edge, each tool has its own set of capabilities, he says. The tools are preset for the job, but can be configured on the fly. The software that supports the tools provides the necessary intelligence to manage the hand-over between shifts, and ensure that production errors are rectified quickly.
Describing the approach Airbus is taking, Boria says: “We do not require live data, but require data to be there at the right time.”
So, to avoid potential errors in production, the tools themselves need to have intelligence at the IoT edge. They run a small piece of agent software that sends a 36 byte message to an HPE Edgeline server, using a non-standard network protocol, which supports a very low data latency of 50 milliseconds.
“This enables an adjustment to be made on the tool, or the operator can be alerted about the error, very quickly, which reduces lost production time,” says Boria. “What is important is to repair or correct a problem before production goes to the next stage.”
Boria says Airbus is an operator-driven company and technology must be deployed as an enabler. This means that digitisation cannot stop aircraft production, or get in the way of operators doing their job.
He also feels that the IoT should be easy to use, especially when deployed on the factory floor. “Nobody reads a book to use Facebook,” he says. “You don’t want to read a manual to use a tool you have used for years.”