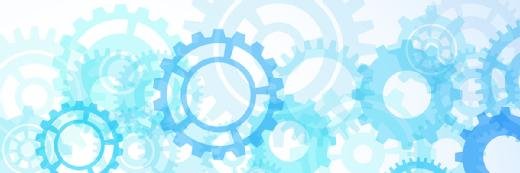
Gearing up for the industrial metaverse
With the hype around the metaverse probably at an all-time low since the former Facebook invented it, it could be argued that its potential is at an all-time high. Where will this potential be exploited and though what tools?
“The industrial and enterprise metaverses are here – this study shows the clear appetite for these technologies such as extended reality and digital twins to achieve business goals. We are already seeing many organisations going above and beyond the planning stages and recognising tangible benefits from their initial implementations.” So said Vincent Douin, executive director of business consulting and business transformation at Ernst & Young, commenting on research by his company in June 2023.
The findings of its The metaverse at work study were clear: across use cases, particularly industrial and enterprise, early metaverse adopters report benefits more often than companies still in the planning phase, with most believing in the power of the metaverse and that metaverse technologies are here to stay. Nearly all (94%) of those yet to begin their metaverse journey plan to do so in the next two years. But where exactly will this journey start and what types of computer tools are set to be deployed to make the on-screen dreams a reality?
The E&Y study is a good place to start. It examined four industry sectors – automotive; industrial goods and manufacturing; transportation, supply chain and logistics; and power and utilities – and attempted to highlight the drivers and potential benefits of metaverse technologies.
The report noted that the enterprise metaverse is driven by demand for better digital collaboration and communication tools, and said it would envelop the core productivity applications that make businesses function and allow for the next generation of virtual connections. It also characterised the industrial metaverse by physical-digital fusion and human augmentation focused on industrial applications. This includes digital representations of physical industrial environments, systems, processes, assets and spaces that participants can control, monitor and interact with.
And digital representations could well be key. In May 2023, Jim Heppelmann, CEO of engineering design and manufacturing software provider PTC, outlined his company’s strategy to evolve from its heritage in computer-aided design (CAD), simulation, built-in product data management (PDM) and connected product lifecycle management (PLM), to support customers – from all parts of industry and process engineering – through the demands of the next generation of digital transformation.
Digital thread linking physical and virtual worlds
Such technologies will be integrated with core design, manufacturing, data management and collaboration technologies as part of what is being referred to as the digital thread that binds together the next generation of digital transformation from concept to design, to manufacture, and ultimately to operation and service. Importantly, this thread will stitch together the physical and virtual worlds to solve spatial problems in engineering, manufacturing and field service operations.
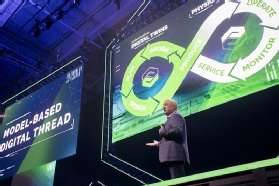
“When product models are reused in downstream processes, and versions and configurations linked together in a way that provides traceability and change control, we call it a model-based digital thread … [which connects] its way from the digital world to the physical world and back again, following the lifecycle of a company’s products,” Heppelmann observed.
“It starts in the digital world with requirements planning and system engineering, which then leads to engineering design, simulation and validation of the product concept, and ultimately to the manufacturing process that converts the digital concept into a physical product… The concept of a model-based digital thread is powerful for every industrial company, but some of our customers are taking it to the next level by overlaying the digital thread concept on their product platform strategy.”
What this means in practice is that with industrial metaverse technology, when a challenge is encountered, engineers can use a connected device to create and capture a spatial digital twin, the metaverse, that digitises the real world of the factory or customer site. A pop-up metaverse, says PTC.
“Knowledge workers can then teleport into this [world] with just a click of a mouse. The front line workers who are physically present, and knowledge workers who are virtually present, see and hear the same real-time experience,” said Heppelmann. “Together they explore spatial problems and access information from the digital thread, such as service instructions, parts, catalogues or IoT [internet of things], then, in many cases, problems can be solved faster than the time it takes to book an aeroplane ticket. Not only does this approach save incredible amounts of time, it is also cost effective and environmentally friendly.”
Tapping into industrial metaverse possibilities
This journey has been demonstrated by PTC customer Burckhardt Compression. Based in Winterthur, Switzerland, the company has the stated mission of creating compression solutions for a sustainable energy future and the long-term success of its customers.
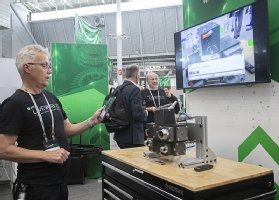
With its brands Burckhardt Compression, Prognost, SAMR Métal Rouge and Shenyang Yuanda Compressor, the company’s customised and modularised compressor systems are used in the chemical/petrochemical, gas transport and storage, hydrogen mobility and energy, and industrial gas sectors, as well as for applications in refinery and gas gathering and processing. It is already pioneering use of industrial metaverse technology.
The company believes the industrial metaverse brings together so many new possibilities, creating interactivity with something of permanence that you can always go back to and add to. Burckhardt describes it as having all of the complexity you want with all of the simplicity you need.
Outlining the difference between traditional engineering and the industrial metaverse, Helmut Draxler, chief digital and information officer at Burckhardt Compression, says: “Today, we have a limited view in what is visible. The metaverse gives us the whole space like a helicopter view. It gives us the possibility to interact with our customers, fast and agile. The industrial metaverse allows us to overcome time, distance and perspective of constantly being in contact.”
In a typical use case, the company points to being able to manage the operations of a tanker at sea, where if there is any incident with machinery, you cannot simply bring in a service engineer, instead using the industrial metaverse with cloud-based PTC technology.
“You can have detailed views and it’s quite simple,” explains Draxler. “The installation is not over weeks or months, it’s minutes or hours. That means we reduce travel time [so] we have a higher efficiency. Also, for the engineer, it’s more convenient. They stay in context, so when [engineers] enter the metaverse, it’s all there, easy to access. And it’s not only related to one person, so it’s a comprehensive history, documentation and everything, that leads them to better service, faster intervention and hierarchical customers.
“All layers work together, from the connectivity to the data flow, the applications, the visualisation,” he adds. “[The metaverse] brings all this brings together and makes it a very interesting user experience. The metaverse is a game-changer for us. It’s about distribution of knowledge. We can distribute the knowledge to new colleagues joining. We can also distribute the knowledge to existing people who have been servicing other machines. It’s a virtual universe of collaboration, and that’s amazing.”
Equipment for delivering information
Amazing, and yet disruptive by the same regard and at the same time. Those driving this game-changing shift in how manufacturing and industry takes place are well aware of the opportunities that this disruption can present. But a key gating factor could well be how, as people, we are able to consume the massive amount of information generated in the industrial metaverse, especially when it comes to being able to support the ability to augment information in front of users to help them either conduct a task more efficiently or provide them with information about what’s happening.
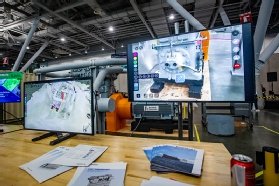
Companies are using smartphones and wearables in use cases including training, maintenance and assembly procedure. Things like the HoloLens, particularly HoloLens 2, but also ruggedised eyewear. Apple has now entered the fray with Vision Pro, which software firms envisage being used as a prototyping tool of choice for developers, as designers can prototype eye gaze and hand pinch interactions.
A general consensus, though, is that currently there is no standout candidate wearable device that is suitable for all sorts of hazardous environments and throughout an eight-hour shift. But it seems this could be just a matter of time. There are reports of a major German automotive manufacturer planning to put augmented reality into its service centres globally any time soon.
Again, it is just a matter of time. And at this particular time, Heppelmann believes industrial companies at large, and not just his company, find themselves in one of the greatest periods for change. It is said a change can do you good – whether physical or virtual, it probably doesn’t matter.
Read more about the industrial metaverse
- Industrial metaverse heralds commercial transformations: Despite the best of intentions, sometimes rebrands just don’t work. Yet while the adoption issues of the metaverse in the consumer market are real, in the industrial world, the metaverse’s payoffs are tangible.
- Enterprise and industrial metaverses exceeding expectations: Across use cases, particularly industrial and enterprise, early metaverse adopters report benefits more often than companies still in the planning phase, with capex reduction and sustainability showing largest difference.
- Alaian, Qualcomm seek out extended reality startups: Collaboration between telco alliance and leading mobile platform provider looks to offer emerging talents in extended reality the ability to accelerate their growth and promote the development of disruptive offerings.
- Siemens aims to pioneer industrial metaverse usage: German engineering giant is exploring industrial metaverse use cases, and the Biosphere Foundation in Devon is proving out Siemens technology.