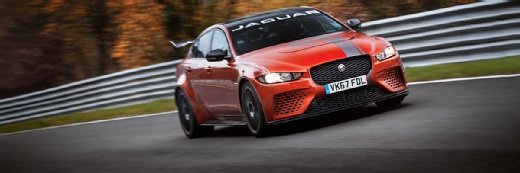
Jaguar Land Rover
Jaguar Land Rover goes live with large-scale retrofit private 5G manufacturing network
Leading UK auto manufacturer goes live with installation of private 5G network at its Solihull plant in project that is part of UK government-backed 5G Innovation Regions programme
As part of its mission to keep pace in a global automotive industry that is being reshaped by electrification and software-defined vehicles, Jaguar Land Rover (JLR) announced in January 2025 that it has embarked on a major enhancement of its connected vehicle ecosystem, and in the latest step of its technology evolution, it has gone live with what it says is the UK’s first retrofit private 5G network in a large-scale manufacturing facility that turns digital theory into reality.
JLR has an overarching strategy to become carbon net zero across its supply chain, products and operations by 2039. Electrification is said to be central to this strategy, and before the end of the decade, its Range Rover, Discovery and Defender collections will each have a pure electric model, while Jaguar will be entirely electric.
The private 5G network at JLR’s Solihull plant is described as having created a unique facility in which the company can test a variety of use cases, obtain the data needed to support business case development, and build a blueprint for wider adoption – not only within JLR, but across the rest of the UK manufacturing industry.
The private network, based on Ericsson 5G technology, currently connects production machinery with a number of Dell edge computing devices and a Litmus Data Ops platform to create a more agile and responsive manufacturing environment for JLR’s Range Rover vehicles that will help production managers turn real-time data insights and simulations into tangible, operational efficiencies.
“5G availability in our manufacturing facilities in the Midlands is essential to JLR’s digital transformation as we enhance the performance of our industrial footprint,” said Stephen Mason, digital operations director at JLR. “As we gear up to the production of our next-generation electric vehicles and their new platforms, the adoption of advanced wireless technologies will improve the scalability, flexibility and resilience of our manufacturing sites.”
The installation forms part of the 5G Innovation Regions (5GIR) Advanced Manufacturing programme. Launched in 2023 by the UK’s Department for Science, Innovation and Technology (DSIT), the 5GIR programme has invited applications into a £40m fund for local authorities across the UK to establish themselves as hubs to drive 5G adoption, with a focus on key sectors where there is local capability and opportunities.
The JLR project is being delivered by West Midlands 5G hothouse WM5G, and aims to streamline the manufacturer’s operations, allowing for what it calls “seamless”, real-time data transmission that will transform its processes.
Read more about private 5G
- SailGP casts off with private 5G for 2025 races: Leading global sailing event taps global comms tech provider for cellular private networks to power connectivity.
- Harwell Science and Innovation Campus deploys private 5G connectivity: Technology laboratories, startups and research institutions at leading UK research facility are set to benefit from private 5G network connectivity.
- Boldyn Networks boosts private 5G with Smart Mobile Labs acquisition: UK shared network infrastructure provider furthers business expansion with strategic purchase of German private 5G network and turnkey applications company.
- Private 5G takes off at Schiphol airport: Ericsson partners with Amsterdam airport to implement a private 5G network as part of Airport 4.0 digital transformation plan supporting use cases such as IoT monitoring and real-time safety.
Going live with private 5G at JLR is regarded by WM5G as a key milestone. “Smart manufacturing has long been heralded as a game changer for the industry,” said 5GIR programme director Jess Ellis. “It has huge potential to improve productivity and unleash capacity across the manufacturing sector, be that by reducing production bottlenecks, predicting and reducing downtime, improving workflow, or ensuring and reviewing quality at every stage of the manufacturing process.
“A huge amount of work has gone into getting the project this far: from clarifying service requirements and developing suitable real-world use cases, to identifying and procuring service providers and coordinating the installation alongside ‘business as usual’. We are proud of the work the whole team has delivered to bring this complex project together.”