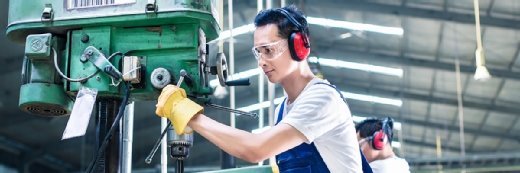
Kzenon - stock.adobe.com
Zeppelin uses Splunk for pre-emptive maintenance
German construction equipment rental firm Zeppelin has been using Splunk to predict when its machinery will need maintenance before it breaks down
Zeppelin dates back to the 1870s when, as the name suggests, it used to manufacture large airships designed by founder Ferdinand von Zeppelin.
After the Second World War, the company changed direction, and is now known mostly for providing construction equipment rentals.
Andreas Zientek, systems engineer at the brand, explains how Zeppelin began using Splunk’s free license in 2010, and now has a 100GB license as the firm absorbs more data from its various systems including VM Ware, an in-house SAP system and various databases.
“All the data these systems produce, like log files or performance data, we index in Splunk,” he says.
Where previously the firm used Splunk for monitoring, reporting, performance analysis and performance optimisation, it began using it for other business and internet of things (IoT) use cases in 2017.
The first IoT use case is for predictive maintenance of the spark plugs in the engines of its rental equipment.
If one of the 20 spark plugs in an engine malfunctions, the engine will fail, and if its customers can’t use the machinery then Zeppelin lose money. “We are collecting data every minute for every single spark plug in the engine,” says Zientek.
Machine learning
Zeppelin has built a machine learning model in Splunk to detect when spark plug failures are about to happen, allowing the firm to send out an engineer to fix the issue before is causes a problem.
Data such as temperature, exhaust temperature and exhaust voltage are taken from the engine and analysed in Splunk to spot patterns in the data that may be indicative of an arising issue.
“Sometimes we can detect a spark plug failure 10 days before, and sometimes it’s only 10 minutes or an hour before,” says Zientek. “It’s still good for our business because we can already send a technician to the customer or we can call the customer to tell them something is wrong and that either they should do something or that we are on the way.”
While the firm has been collecting data such as this for approximately 10 years, it has not been able to use it up until now.
“The joke in my department is that they ask, ‘can we do this in Splunk and how long do you need?’ and I say ‘Yes and 15 minutes’, he says.”
Currently, the firm’s mechanics have access to a Splunk dashboard which allows them to visualise known issues with the engines so they “already know what’s going on” when they arrive on-site to fix it and can make sure they have the right tools with them to complete the repair.
“Normally it would happen, [the customer] would call and hours later someone would be there to fix it,” says Zientek, and tells of a recent incident where a mechanic arrived on-site before the customer had reported a problem.
Data visualisation
While this was initially difficult to implement, it has proven effective, and now the firm is beginning to use machine learning and data visualisation to add value to the data that is collected.
The hope in the future is to use some of the other data points collected by the engines to predict more than just spark plug failure.
“We have 165-200 different metrics which we are collecting for the engines,” says Zientek. “Right now, we’re not using all of them for our model; that’s the future goal to expand this kind of predictive maintenance, but this was the first use case in IoT that was successful, so we are allowed to do more.”
The next step is to use Splunk to keep tabs on the 25,000 Caterpillar machines it loans out to construction firms – all of which are already loading data into the system.
“The goal is to work with this data in Splunk,” he says. “We’ve started to do this, so the data is flowing to Splunk and we want to build condition monitoring around this.”
“This is the next big use case we’re doing, with Splunk and Caterpillar.”
Read more about Splunk
The CAT machines are fitted with telematics boxes which can relay data, and Zientek says he’s already built dashboards in Splunk for these machines so that technicians can look at the metrics collected from these boxes, but that the challenge is building an algorithm that can produce insight from this.
“We are now using this kind of data for some machine learning algorithms,” he says. “The next big step is to find an algorithm so you can analyse the data and get even more from it.”
But maintenance prediction is not the only part of the business Zeppelin is considering using Splunk for, and Zientek says the firm has plans to use data analytics across its business intelligence remit as well as providing some of its C-suite with real-time data on the business.
The CEO level of many businesses, according to Zientek, wants to know if the business is making money.
While this information used to be provided through either an Excel spreadsheet or a business intelligence programme which ran a batch job overnight, CEOs now want this information in real time.
“They want to know how much they’re selling in an hour,” he says. “They want to know who sold it, who is the best seller, who are the customers and what are they buying?”
Now in Zeppelin, the person who sells the most each day gets a prize, and since this figure is in real time, they are selling more rather than holding off depending on when the data for the batch job is sent out.