Materialbedarfsplanung (Material Requirements Planning, MRP)
Was ist Materialbedarfsplanung (Material Requirement Planning, MRP)?
Materialbedarfsplanung (Material Requirement Planning, MRP) ist ein System zur Berechnung der Materialien und Komponenten, die für die Herstellung eines Produkts benötigt werden. Sie besteht aus drei Hauptschritten: Bestandsaufnahme der vorhandenen Materialien und Komponenten, Ermittlung der zusätzlich benötigten Materialien und Komponenten und anschließende Planung ihrer Produktion oder ihres Einkaufs.
Warum ist Materialbedarfsplanung wichtig?
Die Materialbedarfsplanung, die hauptsächlich mit spezieller Software bearbeitet wird, trägt dazu bei, dass die richtigen Materialien für den Produktionsprozess genau dann verfügbar sind, wenn sie benötigt werden, und das zu den niedrigstmöglichen Kosten. MRP verbessert somit die Effizienz, Flexibilität und Rentabilität von Fertigungsabläufen. Es kann die Produktivität von Fabrikarbeitern steigern, die Produktqualität verbessern und Material- und Arbeitskosten minimieren. Materialbedarfsplanung unterstützt Hersteller auch, schneller auf eine erhöhte Nachfrage nach ihren Produkten zu reagieren und Produktionsverzögerungen und Lagerbestände zu vermeiden, die zu Kundenverlusten führen können, was wiederum zu Umsatzwachstum und -stabilität beiträgt.
Materialbedarfsplanung wird von Herstellern weit verbreitet eingesetzt und hat zweifellos maßgeblich zum Wachstum und zur breiten Verfügbarkeit erschwinglicher Konsumgüter beigetragen und damit den Lebensstandard in den meisten Ländern erhöht. Ohne eine Möglichkeit, die komplexen Berechnungen und das Datenmanagement von Materialbedarfsplanungsprozessen zu automatisieren, wäre es für einzelne Hersteller unwahrscheinlich gewesen, ihre Geschäftstätigkeit so schnell auszubauen, wie sie es in den fünfzig Jahren seit der Einführung von Software für die Materialbedarfsplanung getan haben.
Wie funktioniert Materialbedarfsplanung?
Die Materialbedarfsplanung verwendet Informationen aus der Stückliste, Bestandsdaten und dem Produktionsplan, um die erforderlichen Materialien zu berechnen und festzustellen, wann sie im Fertigungsprozess benötigt werden.
Die Stückliste ist eine hierarchische Liste aller Materialien, Unterbaugruppen und anderer Komponenten, die zur Herstellung eines Produkts benötigt werden, zusammen mit ihren Mengen, die jeweils in einer Eltern-Kind-Beziehung dargestellt werden. Das Endprodukt ist das übergeordnete Element an der Spitze der Hierarchie.
Die in der Stückliste aufgeführten Artikel werden entweder als unabhängige Nachfrage oder als abhängige Nachfrage klassifiziert. Ein Artikel mit unabhängiger Nachfrage ist das Endprodukt an der Spitze der Hierarchie. Hersteller bestimmen die Menge, indem sie bestätigte Aufträge berücksichtigen, sowie Marktbedingungen, frühere Verkäufe und andere Indikatoren untersuchen, um eine Prognose zu erstellen, und dann entscheiden, wie viele Artikel hergestellt werden sollen, um die erwartete Nachfrage zu decken.
Abhängige Bedarfsartikel hingegen sind die Rohstoffe und Komponenten, die zur Herstellung des Endprodukts benötigt werden. Bei jedem dieser Artikel hängt die Nachfrage davon ab, wie viele benötigt werden, um die nächsthöhere Komponente in der Stücklistenhierarchie herzustellen.
Die meisten Unternehmen verwenden das MRP-System, um all diese Abhängigkeiten zu verfolgen und zu verwalten und die Anzahl der Artikel zu berechnen, die bis zu den im Master-Produktionsplan angegebenen Terminen benötigt werden. Anders ausgedrückt ist MRP ein Bestandsverwaltungs- und -kontrollsystem für die Bestellung und Verfolgung der Artikel, die für die Herstellung eines Produkts benötigt werden.
Die Vorlaufzeit – der Zeitraum zwischen der Auftragserteilung und der Lieferung des Artikels – ist ein weiteres Schlüsselkonzept in der Materialbedarfsplanung. Es gibt viele Arten von Vorlaufzeiten. Zwei der häufigsten sind die Materialvorlaufzeit (die Zeit, die benötigt wird, um Materialien zu bestellen und zu erhalten) und die Fabrik- oder Produktionsvorlaufzeit (die Zeit, die benötigt wird, um das Produkt herzustellen und zu versenden, nachdem alle Materialien vorhanden sind). Die Kundenvorlaufzeit bezeichnet die Zeit zwischen der Kundenbestellung und der endgültigen Lieferung. Das MRP-System berechnet viele dieser Vorlaufzeiten, aber einige werden von den Betriebsleitern ausgewählt und manuell eingegeben.
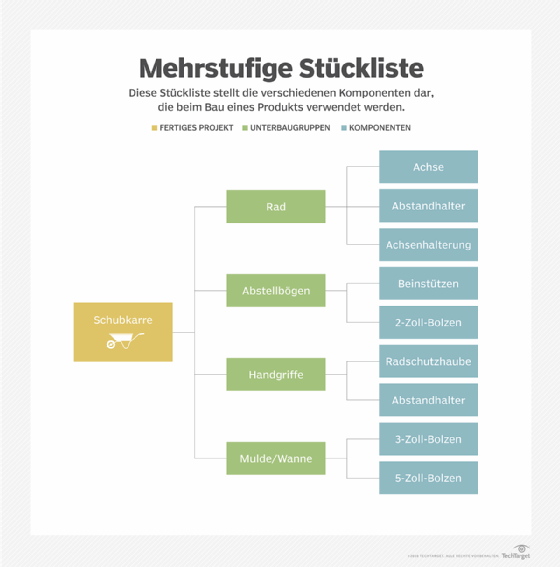
Materialbedarfsplanung in der Fertigung
Die Materialbedarfsplanung ist für die Effizienz, Effektivität und letztlich die Rentabilität eines Fertigungsbetriebs von entscheidender Bedeutung. Ohne die richtigen Rohstoffe und Komponenten können Hersteller nicht darauf hoffen, die Produktnachfrage zu optimalen Kosten und in optimaler Qualität zu decken. Sie sind auch weniger in der Lage, auf Nachfrageschwankungen durch Anpassung der Produktion zu reagieren.
Die Materialbedarfsplanung kann auch dazu beitragen, dass die späteren Produktionsphasen, wie Montage und Verpackung, reibungsloser und vorhersehbarer ablaufen, indem sie die meisten Unsicherheiten in Bezug auf den Lagerbestand beseitigt und den Zeitaufwand für dessen Verwaltung minimiert.
Die Materialbedarfsplanung ist sowohl in der diskreten Fertigung nützlich, bei der die Endprodukte einzelne zählbare Artikel sind, wie Schrauben, Unterbaugruppen oder Autos, als auch in der Prozessfertigung, bei der Massenprodukte wie Chemikalien, Softdrinks und Reinigungsmittel entstehen, die nicht einzeln gezählt oder leicht in ihre Bestandteile zerlegt werden können.
Vorteile der Materialbedarfsplanung
Das Hauptziel der Materialbedarfsplanung besteht darin, sicherzustellen, dass Materialien und Komponenten bei Bedarf im Produktionsprozess verfügbar sind und die Fertigung planmäßig erfolgt. Weitere Vorteile der Materialbedarfsplanung sind:
- kürzere Lieferzeiten für Kunden und damit eine höhere Kundenzufriedenheit
- geringere Lagerhaltungskosten
- effektive Bestandsverwaltung und -optimierung – durch den Erwerb oder die Herstellung der optimalen Menge und Art von Beständen können Unternehmen das Risiko von Fehlbeständen und deren negative Auswirkungen auf Kundenzufriedenheit, Umsatz und Einnahmen minimieren, ohne mehr als nötig für Bestände auszugeben
- verbesserte Fertigungseffizienz durch genaue Produktionsplanung und -terminierung zur Optimierung des Einsatzes von Arbeitskräften und Ausrüstung
- verbesserte Arbeitsproduktivität
- wettbewerbsfähigere Produktpreise
Nachteile von MRP
Materialbedarfsplanung hat aber auch Nachteile, darunter:
- Überangebot an Lagerbeständen. Materialbedarfsplanung ist zwar darauf ausgelegt, angemessene Lagerbestände zu den erforderlichen Zeitpunkten sicherzustellen, doch Unternehmen können versucht sein, mehr Lagerbestände zu halten als nötig, wodurch die Lagerhaltungskosten in die Höhe getrieben werden. Ein MRP-System erkennt Engpässe früher, was dazu führen kann, dass die Losgrößen und Vorlaufzeiten der Lagerbestände überschätzt werden, insbesondere in den ersten Tagen der Bereitstellung, bevor die Benutzer die Erfahrung sammeln, die tatsächlichen benötigten Mengen zu kennen.
- Mangelnde Flexibilität. Materialbedarfsplanung ist auch etwas starr und vereinfacht die Berücksichtigung von Vorlaufzeiten oder Details, die sich auf den Master-Produktionsplan auswirken, wie zum Beispiel die Effizienz der Fabrikarbeiter oder Probleme, die die Lieferung von Materialien verzögern können.
- Anforderungen an die Datenintegrität. MRP ist in hohem Maße auf genaue Informationen über wichtige Eingaben angewiesen, insbesondere über Nachfrage, Bestand und Produktion. Wenn eine oder zwei Eingaben ungenau sind, können sich Fehler in späteren Phasen vergrößern. Datenintegrität und Datenverwaltung sind daher für die effektive Nutzung von Materialbedarfsplanungssystemen unerlässlich.
Um diese Mängel der Materialbedarfsplanung zu beheben, verwenden viele Hersteller eine APS-Software (Advanced Planning and Scheduling), die mit ausgefeilten mathematischen und logischen Verfahren genauere und realistischere Schätzungen der Durchlaufzeiten liefert. Im Gegensatz zu den meisten Materialbedarfsplanungssystemen berücksichtigt die APS-Software die Produktionskapazität, was sich erheblich auf die Verfügbarkeit von Materialien auswirken kann.
Geschichte der Materialbedarfsplanung
Die Anfänge der Materialbedarfsplanung liegen zu Beginn des 20. Jahrhunderts in der Entwicklung neuer Modelle zur Fertigungsoptimierung. Im Jahr 1913 entwickelte der amerikanische Produktionsingenieur Ford Whitman Harris die Berechnung der wirtschaftlichen Bestellmenge, die Menge, die die Kosten für die Bestellung und Lagerung eines Gutes minimiert. Gleichzeitig zeigte das von Henry Ford entwickelte Massenproduktionssystem, wie wertvoll eine strenge Kontrolle des Materialflusses durch ein Fließband ist. Ein weiterer wichtiger Faktor für die industrielle Effizienz waren die wissenschaftlichen Managementtheorien von Frederick Taylor, die Techniken zur Produktionsplanung und -steuerung sowie zur Verbesserung der Effizienz des Materialhandlings beinhalteten.
Mit dem Aufkommen von Computern begann für Systeme zur Optimierung des Fertigungsprozesses ein neues Zeitalter. Als in den 1950er Jahren Großrechner auf den Markt kamen, begannen Programmierer in Fertigungsunternehmen mit der Entwicklung maßgeschneiderter Software zur Verwaltung von Stücklisten, Lagerbeständen, Produktion und Planung.
Der moderne Name für diesen Bereich kam jedoch erst in den 1960er Jahren auf. Damals setzte sich eine kleine Gruppe einflussreicher Ingenieure für ein integriertes System der computergestützten Planung ein, das sie Material Requirement Planning (MRP), auf Deutsch Materialbedarfsplanung, nannten. 1964 entwickelte und formalisierte der IBM-Ingenieur Joseph Orlicky MRP, nachdem er das Toyota-Produktionssystem studiert hatte, das als Vorbild für die schlanke Produktion (Lean Production) diente. 1967 schrieb Orlickys IBM-Kollege Oliver Wight zusammen mit George Plossl, einem Maschinenbauingenieur und Unternehmensberater, ein Buch über Produktions- und Bestandskontrolle. Die drei arbeiteten weiterhin zusammen und werden heute in der Regel als die Pioniere des MRP bezeichnet.
Es ist wichtig zu wissen, dass Materialbedarfsplanung und schlanke Produktion nicht dasselbe sind, obwohl sie in Orlickys Pionierarbeit miteinander in Verbindung stehen. Tatsächlich werden sie von vielen Praktikern als gegensätzlich angesehen, obwohl einige sagen, dass Materialbedarfsplanung bei der schlanken Produktion unterstützen kann. Materialbedarfsplanung wird als Push-Produktionsplanungssystem betrachtet – der Lagerbedarf wird im Voraus festgelegt und die Waren werden produziert, um den prognostizierten Bedarf zu decken –, während Lean Production ein Pull-System ist, bei dem nichts hergestellt oder gekauft wird, ohne dass ein tatsächlicher – nicht prognostizierter – Bedarf nachgewiesen wird.
Orlickys Ideen verbreiteten sich nach der Veröffentlichung seines Buches Material Requirements Planning: The New Way of Life in Production and Inventory Management im Jahr 1975 schnell im gesamten Fertigungssektor. Anfang der 1980er Jahre gab es Hunderte von kommerziellen und selbst entwickelten MRP-Softwareprogrammen.
Materialbedarfsplanung erhielt in den 1970er Jahren auch durch die Bildungsbemühungen der American Production and Inventory Control Society (APICS) einen großen Aufschwung, nachdem Orlicky, Plossl und Wight die Vereinigung dazu gedrängt hatten, für MRP zu werben. APICS wurde zur Hauptquelle für MRP-Schulungen und -Zertifizierungen und nimmt diese Rolle auch heute noch ein, wobei sie sich im Laufe der Jahrzehnte auf die Bereiche Betriebsführung und Lieferkettenmanagement ausgeweitet hat.
Orlicky starb 1986. Eine zweite Auflage seines Buches, aktualisiert von Plossl, wurde 1994 veröffentlicht. Die aktuelle Version, Orlickys Material Requirements Planning, Third Edition, ist eine Aktualisierung von 2011 durch die Berater Carol Ptak und Chad Smith. Es enthält zusätzliche Ratschläge zur Verwendung der Materialbedarfsplanung für einen nachfrageorientierten Planungsprozess, bei dem die Materialanforderungen anhand tatsächlicher Verkaufsaufträge und nicht anhand der typischen MRP-Methode einer Verkaufsprognose berechnet werden. Dieser neuere Pull-Ansatz, der als nachfrageorientierte Materialbedarfsplanung (Demand-driven Material Requirements Planning, DDMRP) bezeichnet wird, ist umstritten und wird von einigen als Verstoß gegen wichtige von Orlicky festgelegte Grundsätze angesehen.
MRP versus ERP
Eine Erweiterung von MRP, die 1983 von Wight entwickelt wurde und als Manufacturing Resource Planning (MRP II) bezeichnet wird, erweiterte den Planungsprozess um andere Ressourcen im Unternehmen, wie zum Beispiel Finanzen, und fügte Prozesse für Produktdesign, Kapazitätsplanung, Kostenmanagement, Fertigungssteuerung und Vertriebs- und Betriebsplanung hinzu, neben vielen anderen.
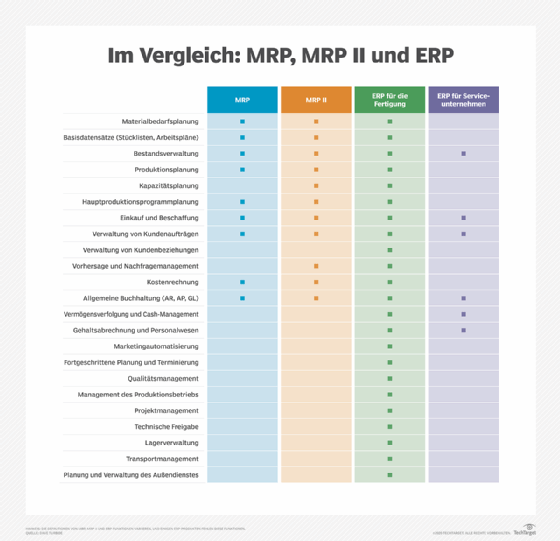
1990 prägte das Analystenunternehmen Gartner den Begriff Enterprise Resource Planning (ERP), um eine noch umfassendere und allgemeinere Art von MRP II zu bezeichnen, die andere wichtige Funktionen eines Unternehmens wie Buchhaltung, Personalwesen und Lieferkettenmanagement berücksichtigte, die alle in einer zentralen Datenbank verwaltet wurden. Sowohl MRP als auch MRP II gelten als direkte Vorgänger von ERP.
ERP breitete sich schnell auf andere Branchen aus, darunter Dienstleistungen, Banken und Einzelhandel, die keine MRP-Komponente benötigten. MRP ist jedoch nach wie vor ein wichtiger Bestandteil der von Herstellern verwendeten ERP-Software.