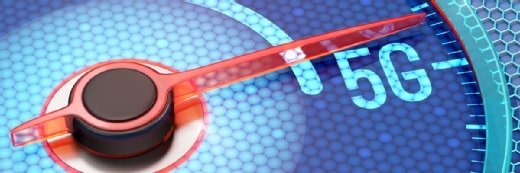
iaremenko - stock.adobe.com
5G in der Fertigung treibt Wandel in gesamter Industrie
5G in der Fertigung steht in den Startlöchern. Doch nur wenige können exakt vorhersagen, wie die digitale Transformation sich auf den operativen Betrieb auswirken wird.
Neben erhöhter Konnektivität, Zuverlässigkeit an Remote-Standorten und Datensicherheit verspricht 5G neue Möglichkeiten für Smart Manufacturing und industrielles IoT.
Ungeplante Downtime, Equipment-Ausfälle und Produktionsfehler in der Fertigungsumgebung können zu Nachwirkungen in Form von Schadensbegrenzung, unzufriedenen Kunden, Störungen der Lieferkette und sogar Umsatzeinbußen führen. Indem sie eine unvermeidbare 5G-basierte Zukunft akzeptieren und sich darauf vorbereiten, können Hersteller diese Risiken vermeiden und Industrie-4.0-Entwicklungen beschleunigen.
Gleichzeitig bietet sich die Möglichkeit, andere Kerntechnologiebereiche wie KI, Robotics, Computer Vision (maschinelles Sehen, Bildanalyse) und Bewegungssteuerung einzubeziehen. Laut dem Bericht 5G in industrial operations von CapGemini (PDF) betrachten 75 Prozent der Industrieunternehmen 5G als kritisch in ihren Bestrebungen um eine digitale Transformation.
5G in der Fertigung kann Organisationen dabei helfen, ihre aktuellen industriellen Verfahren in Prozesse umzuwandeln, die von der Geschwindigkeit der Informationsübertragung und raschem, breit aufgestelltem Edge Computing profitieren.
Fabrikautomation wird sich Nachfrageänderungen anpassen
Derzeit experimentieren Hersteller mit Proofs of Concept (PoC) oder wählen automatisierte Maschinen und Prozesse, die zu größerer Effizienz und besseren operativen Datensätzen beitragen. Diese Bemühungen sind häufig unzusammenhängend, langsam oder lassen sich nicht skalieren, weil sie nicht in großem Maßstab im gesamten Produktionsbetrieb koordiniert werden. Der Mensch muss hier immer noch eingreifen.
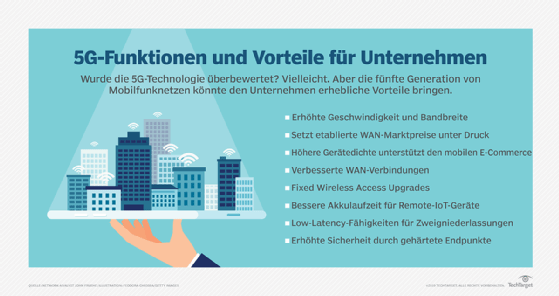
In einer 5G-Zukunft wird der Betrieb von hochautomatisierten, roboterhaften und vernetzten Maschinen durch eine zentrale Steuerung koordiniert, um die Produktionsleistung der Hersteller zu optimieren. 5G in der Fertigung wird schnelle Datentransfers von Maschinensensoren mit KI, Computer Vision und Edge Computing vorantreiben, um Fabriken so zu gestalten, dass sie sich Nachfrageänderungen automatisch – und sogar vorausschauend – anpassen.
Die Fabriken werden den Workflow entsprechend ändern und das Troubleshooting auf die maschinelle Downtime ausrichten. Hersteller, die 5G nutzen, werden eine Reihe von Vorteilen für sich entdecken: Kostensenkungen, gesteigerte Effizienz, besserer Mix und passende Bedarfsdeckung, einfachere Produktanpassung, bessere Produktionsauslastung und mehr Durchsatz sowie leichtere Neukonfiguration von Maschinen.
5G in der Fertigung erhöht die Effizienz des Produktions-Monitorings
Hersteller schicken Standortmanager zu verschiedenen Gebäuden und anderen Remote-Standorten, um Equipment und Maschinen zu inspizieren, den Zustand von Ausrüstung und Werkzeugen zu überprüfen und manuell Diagnosen durchzuführen. Ein Netzwerk von IoT-Sensoren überwacht das Equipment und kennzeichnet potenzielle oder aktuelle Probleme.
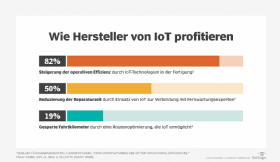
Hersteller nutzen Drohnen, die mit Kameras und Computer-Vision-Technologie ausgerüstet sind, um alle anderen Problembereiche aufzuspüren. IoT-Sensoren können per KI Geräusche erkennen, die auf Schwierigkeiten hindeuten.
Bei dem Ganzen helfen zwei 5G-Netzwerke: ein lokales mit großer Bandbreite, damit Sensoren und Drohnen mit der zentralen Verarbeitungssoftware kommunizieren können, und eines mit geringer Bandbreite und größerem Radius, das bei Bedarf den Remote-Standort wieder mit dem Kontrollzentrum verbindet.
Dank 5G in der Fertigung werden Organisationen Ressourcen und die Zeit der Mitarbeiter besser nutzen und die Zahl der Standortinspektionen durch Menschen reduzieren. Die Produktivität der Standortinspektionen lässt sich verbessern, da die Problembereiche vorab bekannt sind. Sicherheitsrisiken im Produktionsbereich werden reduziert und die Produktivität steigt.
Training der Mitarbeiter mit Augmented Reality
Hersteller investieren Zeit und Ressourcen, um neue Mitarbeiter in persönlichen Trainings mit Legacy-Materialien und -Medien auf ihre Aufgaben vorzubereiten. Da viele Hersteller eine hohe Mitarbeiterfluktuation erleben, können die hohen Investitionen in die Ausbildung im Laufe der Zeit zu einem größeren Produktivitätsverlust führen, wenn immer wieder neue Mitarbeiter eingestellt werden müssen.
Eines der größten Versprechen von 5G ist die niedrige End-to-End-Latenz – bis unter eine Millisekunde. Das bietet Gelegenheit für neue Trainingsmethoden der Mitarbeiter per erweiterter Realität (Augmented Reality) und virtueller Realität (Virtual Reality).
Augmented Reality (AR) und Virtual Reality (VR) können ein schrittweises Training in Echtzeit ermöglichen. Die zu schulenden Mitarbeiter führen Aktionen im Sichtfeld durch und können währenddessen erkennen, ob sie etwas ändern müssen, um Anpassungen vorzunehmen oder Fehler zu vermeiden.
Eine schnelle 5G-Verbindung mit geringer Latenz verbindet das AR- und VR-Headset mit High Performance Computing, das sich am Netzwerk-Edge befindet. Auf diese Weise gibt es keine Verzögerungen, wenn sich der Mitarbeiter bewegt. Für die Hersteller bedeutet das eine kürzere Einarbeitungszeit, größere Verfahrensgenauigkeit, effizientere Jobwechsel, bessere Anpassung, weniger Unfälle und verbessertes Performance Monitoring.
5G verbessert das Asset Tracking mit vernetzten Sensoren
In einem Produktionsbereich oder auf einer Baustelle können Werkzeuge leicht verloren gehen oder gestohlen werden. Heute müssen Standortleiter Fertigungs-Assets manuell nachverfolgen und sie in festgelegten Intervallen inventarisieren. Das nimmt wertvolle Zeit und Ressourcen in Anspruch, ohne garantierte Genauigkeit. Auch die Arbeiter verlieren bei der Suche nach Werkzeug Zeit.
Die Hersteller nutzen Software, die mit IoT-Sensoren auf wichtigem Equipment verbunden ist und erkennen kann, wenn diese Ausrüstung zweckentfremdet wurde, repariert oder ersetzt werden muss. Arbeiter können mit den Equipment-Daten Werkzeug effizienter lokalisieren und ihre Arbeit wieder aufnehmen.
5G-Netzwerke mit geringer Leistung verbinden sich mit Asset-Sensoren und nutzen mehrere Antennen sowie Signaltriangulation, um festzustellen, ob Ausrüstungsgegenstände an anderer Stelle abgelegt wurden. Bessere Netzwerkverbindungen werden das Aufspüren von Assets und die Produktivität verbessern, Verluste am Standort reduzieren, für eine genauere Inventarisierungsverwaltung sorgen und bessere Daten liefern, um den künftigen Asset-Bedarf zu planen.
Wie Hersteller sich auf die neue 5G-Welt vorbereiten können
Die Hersteller müssen sich die folgenden Fragen stellen, um sich auf die bevorstehenden Änderungen an ihren Betriebsabläufen durch 5G einzustellen:
- Welchen Proof of Concept, der sich mit 5G noch weiter verbessern lässt, kann die Organisation heute starten?
- Welche wichtigen Standards oder Spezifikationen im Zusammenhang mit 5G erfordert der Proof of Concept? Was ist mit anderen Anwendungsfällen?
- Welche kritischen Anforderungen – zum Beispiel Sicherheit oder Edge-Verarbeitung – sind Voraussetzungen für den Proof of Concept oder zukünftige Anwendungsfälle?
- Welche Partner können 5G-bezogene Innovation, Bereitstellung, Verteilung und Analytics beschleunigen?
- Welche Software, Entwickler-Tools und Hardware wird 5G-Anwendungsfälle beschleunigen und Investitionen schützen?