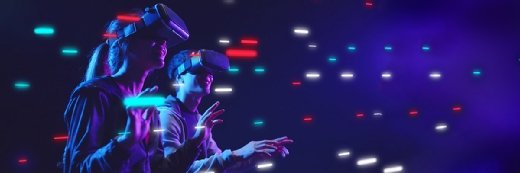
DIgilife - stock.adobe.com
Industrial Metaverse: neuer Weg zur nachhaltigen Produktion
Das Industrial Metaverse ist ein kollektiver virtueller Raum, der alle virtuellen Welten, Internet und erweiterte Realität umfasst. Wie sich dessen Potenzial ausnutzen lässt.
Die Industrie ist in Deutschland derzeit für etwa 22 Prozent der Treibhausgasemissionen verantwortlich. Eine grundlegende Transformation der industriellen Produktionsprozesse ist notwendig, um eine klimaneutrale Industrie zu erreichen.
Dies erfordert ein Umdenken der Produktionsketten und -standorte über Branchen hinweg und den Einsatz innovativer Technologien wie dem Industrial Metaverse. Die virtuelle oder erweiterte Realität, die bereits für die Erstellung von Prototypen und die Planung effizienter Produktionsstätten genutzt wird, bietet hinsichtlich der Nachhaltigkeit ein enormes Potenzial.
Digitale Zwillinge sind nur der Anfang
Ein Teil des Industrial Metaverse wird bereits häufig verwendet: der digitale Zwilling. Die hochpräzisen virtuellen Nachbildungen eines physischen Objekts, Systems oder Prozesses werden zur Leistungskontrolle, Prognose von Problemen oder Durchführung von Experimenten in einer sicheren Umgebung eingesetzt – insbesondere in Industrien, in denen Experimente mit realen Äquivalenten kostspielig oder riskant sein könnten.
Das Industrial Metaverse hingegen erweitert das Konzept des digitalen Zwillings erheblich. Es ist ein kollektiver virtueller Raum, der alle virtuellen Welten, das Internet und die erweiterte Realität beinhaltet. Es handelt sich um eine immersive, interaktive Umgebung, in der Menschen sich treffen, arbeiten und spielen können. In Bezug auf die Industrie schafft das Metaverse einen Raum, in dem digitale Zwillinge nicht nur existieren, sondern auch miteinander interagieren können. Einzelne digitale Zwillinge können zu einem größeren Metaverse von miteinander vernetzten digitalen Zwillingen fusionieren, die auf einem gemeinsamen Datensatz arbeiten. Dies ermöglicht komplexe Simulationen und Vorhersagen in einer Größenordnung, die mit isolierten digitalen Zwillingen nicht erreichbar wäre.
Datengetriebene Kreislaufwirtschaft
In einem Industrial Metaverse kann der digitale Zwilling nicht nur für die virtuelle Simulation des eigentlichen Produktes, sondern für die des gesamten Produktionsprozess genutzt werden. Dieser Prozess umfasst die virtuelle Planung von Produktionslinien und sogar ganzen Fabriken, basierend auf den Produkteigenschaften – und das alles, bevor ein einziges Teil der Anlage physisch gebaut wird. Produktflüsse, Aufgaben der verschiedenen Roboter und deren optimale Platzierung können simuliert und getestet werden, um Kollisionen zu vermeiden.
![]()
„Um das volle Potenzial des Industrial Metaverse zu nutzen, muss der Datenfluss von der eigentlichen Produktion oder dem Produkt selbst bis hin zur Cloud sichergestellt werden.“
Thomas Kräuter, intive
Hier entsteht Potenzial für die Planung nachhaltiger Produktionsprozesse. Die Simulation aller Arbeitsbedingungen für Menschen, Roboter, Produktionslinien und sogar ganze Fabriken sichert, dass die reale Produktion wie geplant verläuft. Mithilfe der virtuellen Modelle können Lösungen gefunden werden, um Abfall zu vermeiden, Energie zu sparen und den Einsatz alternativer Materialien zu simulieren.
Über die Produktion hinaus lässt sich der ganze Produktlebenszyklus im Industrial Metaverse abbilden. Was passiert mit dem Produkt nach seinem Einsatz? Wie können die einzelnen Teile oder Materialien weiter- oder wiederverwendet werden? Mit der Integration von Daten über den gesamten Lebenszyklus eines Produkts lässt sich eine Kreislaufwirtschaft planen und umsetzen.
Echtzeitüberwachung durch OT und IT im Einklang
Um das volle Potenzial des Industrial Metaverse zu nutzen, muss der Datenfluss von der eigentlichen Produktion oder dem Produkt selbst bis hin zur Cloud sichergestellt werden. Alle Feldgeräte und Steuereinheiten, die auf dem Shopfloor operieren, erzeugen natürlich eine Vielzahl von Daten. Werden diese Daten aus der physischen Welt mit denen der digitalen – sprich die Operational Technology (OT) mit der Information Technology (IT) nahtlos miteinander verbunden, können Risiken und Veränderungen in Echtzeit evaluiert werden.
Durch die ständige Synchronisation der beiden Welten können potenzielle Risiken erkannt und Prognosen getroffen werden, um den Betrieb zu optimieren und Störungen zu minimieren. Darüber hinaus ermöglicht die direkte Verbindung von OT und IT den Unternehmen, flexibler auf Veränderungen zu reagieren und vorausschauend Wartungsarbeiten oder Anpassungen durchzuführen.
Dies ist besonders in KRITIS-Unternehmen (Kritische Infrastrukturen) von Bedeutung, in denen jede Änderung erhebliche Auswirkungen auf Mensch und Umwelt haben kann. Ein praxisnahes Beispiel dafür ist die Überwachung und Verwaltung eines Abwassersystems. Blockaden im Abwassersystem können zur Verschmutzung von Flüssen und Wasserstraßen führen.
Mit Unterstützung von Daten wie Echtzeit-Niederschlagsdaten sowie Daten von Sensoren im Abwassersystem können diese Probleme effektiv angegangen werden. Ein KI-System nutzt diese Daten dann, um Probleme wie Blockaden durch grobe Verschmutzungen zu prognostizieren, bevor sie auftreten. Der Wasserversorgungsunternehmer wird über die Stellen informiert, an denen Blockaden am wahrscheinlichsten auftreten. So können im realen Umfeld Ingenieure Probleme inspizieren und beheben, bevor sie eintreten. Durch die Verbindung von OT und IT kann somit eine effektive Echtzeitüberwachung und -steuerung kritischer Infrastrukturen erreicht werden.
Über den Autor:
Thomas Kräuter ist seit 2021 Chief Technology Officer bei intive. Als Group CTO treibt er das Wachstum des Unternehmens voran, vor allem in den Bereichen Automotive, Technology, Media & Communications, Fintech, Retail und Digital Products.
Die Autoren sind für den Inhalt und die Richtigkeit ihrer Beiträge selbst verantwortlich. Die dargelegten Meinungen geben die Ansichten der Autoren wieder.