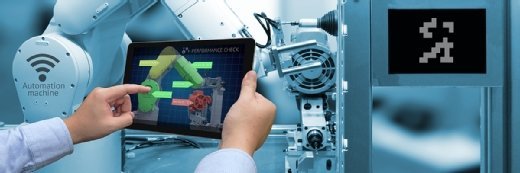
zapp2photo - Fotolia
Industrie wendet sich verstärkt Digital-Twin-Technologien zu
Von Design bis Predictive Analytics: Digital Twins kommen immer häufiger zum Einsatz. Ein Überblick, wie Digital Twins verschiedenen Branchen helfen können.
Mit dem Aufblühen des digitalen Zeitalters erschien es fast unvermeidlich, dass ein Teil dessen, was in der physischen Welt existierte, im digitalen Bereich zum Leben erwacht, und dass diese Nachbildung letztendlich auch einen geschäftlichen Wert erhält.
Das Konsumuniversum wird zunehmend digitalisiert – E-Books und digitale Musik sind überall – und der 3D-Druck hat die Digitalisierung zu einer zweispurigen Straße gemacht. Das Stichwort heißt: Digital Twins (digitale Zwillinge).
Verschiedene Definitionen von Digital Twins
Die Nennwertdefinition des Begriffs Digital Twin ist eine digitale Instanziierung eines realen physischen Assets. Ein Beispiel hierfür ist das 3D-Druckverfahren: Eine digitale Instanziierung eines Objekts wird verwendet, um das Objekt tatsächlich zu erzeugen. Unter Verwendung älterer Terminologien kann man sich einen Digital Twin als eine Simulation von etwas Realem vorstellen.
In einer Präsentation des GE Global Research Center definiert Colin Parris, Vice President of Software Research bei GE, einen digitalen Zwilling als „ein lebendiges Modell von etwas, das ein Geschäftsergebnis liefert“ und operationalisiert das Konzept in der Praxis.
Gartner definiert einen digitalen Zwilling als „ein dynamisches Softwaremodell eines physischen Dings oder Systems“ – die Schlüsselwörter sind Dynamik und System. Die digitale Zwillingstechnologie ist so wichtig, dass sie einen Platz unter den Top 10 Strategic Technology Trends for 2017 von Gartner eingenommen hat.
Die Ursprünge digitaler Zwillingstechnologie
Digitale Zwillinge sind nicht neu – sie gibt es schon seit mehr als 15 Jahren – und sie sind nicht speziell eine Innovation aus dem Geschäftsleben.
Tatsächlich war die Schaffung digitaler Repräsentationen physischer Objekte der Notwendigkeit der NASA geschuldet, extraterrestrisch Umgebungen zu modellieren, um Hardware hierfür zu bauen. Da ein Roboter auf dem Mars nicht in Echtzeit überwacht werden kann, war es für die NASA wichtig, die Umgebung als digitale Simulation zu modellieren, während sie den Roboter entwarf und baute, um sicherzustellen, dass er beim ersten Mal richtig funktioniert.
Diese Überbrückung der physischen und digitalen Sphären ermöglicht die Modellierung des Verhaltens und der Lebenszyklen von Objekten im physischen Raum. Im Zeitalter des Internet der Dinge (IoT) und der Cloud erlaubt es diese Methode, digitale Modelle ständig mit realen Daten aus der physischen Welt zu aktualisieren. Das physische Objekt (oder der Prozess) und sein digitaler Zwilling verbessern sich im Laufe der Zeit deutlich. Und die Anwendungsmöglichkeiten dieses Konzepts sind vielfältig.
Ein geschäftlicher Imperativ für digitale Zwillinge
In einem Forbes-Artikel beschreibt Thomas Kaiser, Senior Vice President of IoT bei SAP, digitale Zwillinge als eine entscheidende Grundlage für vernetzte Produkte und Services.
„Unternehmen, die nicht reagieren, werden zurückgelassen. Diejenigen, die digitale Zwillinge annehmen, haben die Möglichkeit, Kundenbedürfnisse besser zu verstehen, ihre Produkte und Dienstleistungen kontinuierlich zu verbessern und sogar neue Geschäftsmodelle zu identifizieren, die ihnen Wettbewerbsvorteile verschaffen“, erläutert Kaiser.
Tatsächlich hat IoT die digitale Zwillingstechnologie in den Vordergrund gerückt. Die Fähigkeit von realen Objekten, Informationen aus sich selbst und ihrer Umgebung zu sammeln und diese in Echtzeit über das Internet weiterzugeben, macht Digital Twins zu einem unverzichtbaren Bestandteil der prädiktiven Analytik für alle Produkte und Prozesse, die die IoT-Technologie nutzen. Mit anderen Worten, das Internet der Dinge und die digitalen Zwillinge sind füreinander bestimmt.
Unzählige Einsatzszenarien für digitale Zwillinge
Während sich das Internet der Dinge innerhalb und über Branchen hinweg ausweitet, werden sich digitale Zwillinge ebenfalls verbreiten – und ihre Nutzung wird sich entsprechend der Nutzung des Internet der Dinge ausbreiten. Hier nur einige Beispiele:
Branchenübergreifende Datenerhebung und –analyse: Der Stand der Technik in der Produkt- und Dienstleistungsentwicklung war vor digitalen Zwillingen reaktiv, nicht proaktiv.
„Wenn ein Asset fehlschlägt oder kurz davor ist, zu versagen, sammeln die meisten Industrieunternehmen Daten, ohne wirklich zu wissen, welche Daten sie sammeln sollen“, erläutert Parris. „Dies sind unstrukturierte Daten. Das Unternehmen konfiguriert das Datenerfassungs- und Analysemodell in der Folge so um, dass es Sinn macht, die Daten zu erfassen und den Prozess zu verfeinern, bevor es ihn erneut ändern muss, wenn weitere Probleme auftauchen. Es ist ein statisches Lese- und Reaktionsmodell.“
Digitale Zwillinge beseitigen dieses statische Modell und ersetzen es durch ein dynamisches Modell – ein lebendiges Modell, so Parris. Das Rätselraten wird aus der Datenerhebung entfernt, und die gesammelten Daten werden zur Vorbeugung und nicht zur Diagnose nach einem Ausfall verwendet.
Prototyping: Die Digital-Twin-Technologie ermöglicht virtuelles Prototyping – die digitale Erstellung eines Produkts oder einer Dienstleistung, bevor sie physisch instanziiert wird – sowie die Simulation der beabsichtigten Umgebung und des Betriebs. Diese Art des Prototyping ist nicht nur schneller und billiger, sondern letztlich auch präziser, was zu einer höheren Qualität des Produkts oder der Dienstleistung führt.
Im Außendienst: Die Kombination von IoT und digitalen Zwillingen kann zu Predictive Maintenance führen, das heißt die Fähigkeit zu wissen, dass eine Komponente ausfallen wird, bevor sie tatsächlich ausfällt. Der Außendienst kümmert sich in diesem Fall darum, ein Bauteil vor dem Ausfall auszutauschen, und nicht, um bereits ausgefallene Teile zu ersetzen beziehungsweise das zu reparieren, was infolge des Ausfalls defekt ist.
Im industriellen IoT (IIoT): Industrial IoT eröffnet neue Möglichkeiten bei komplexitätsbelasteten Produkten und Prozessen. Flugzeugmotoren, Fabrikroboter und andere komplexe Maschinen sind schwierig zu modellieren, da sie einzelne Komponenten und Prozesse kombinieren, die unerwartet interagieren können. Es ist schwierig, diese Wechselwirkungen bereits in der Entwurfsphase vorherzusehen.
Durch den Einsatz von Industrial IoT (wobei der Flugzeugmotor oder der Fabrikroboter viele Sensoren enthält) in Kombination mit digitalen Zwillingen lassen sich Interaktionen zwischen Komponenten und Prozessen wesentlich einfacher lokalisieren – und anschließend planen. Und diese Daten sorgen nicht nur für ein besseres Design, sondern fließen auch in den oben erwähnten Predictive-Maintenance-Prozess ein.
Digitale Zwillinge sind sicherlich da, um zu bleiben. Gartner prognostiziert, dass sie innerhalb von drei bis fünf Jahren Milliardenbeträge erreichen werden.
Folgen Sie SearchEnterpriseSoftware.de auch auf Twitter, Google+, Xing und Facebook!