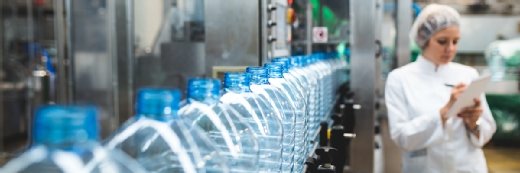
hedgehog94 - stock.adobe.com
Die Herausforderung Predictive Maintenance umsetzen
Im Zuge der Digitalisierung der Industrie wechseln immer mehr Betriebe von der klassischen Wartung zu einer bedarfsorientierten Routine. Das bedarf aber einer guten Vorbereitung.
Condition Based Monitoring beschreibt die kontinuierliche Überwachung von Maschinen im Hinblick auf ihre betriebskritischen Werte. Fast alle modernen Fertigungsmaschinen verfügen über eine Vielzahl an Sensoren, die durchgehend Daten über Temperaturen, Drücke, Drehungen, Spannung etc. sammeln. Übertritt einer dieser Werte über einen längeren Zeitraum einen Schwellenwert, deutet dies auf einen Fehler hin, der die Funktion und die Lebensdauer der Maschine negativ beeinflussen kann und das System gibt eine Warnmeldung heraus.
Unter Predictive Maintenance (vorausschauende Wartung), versteht man die Instandhaltung von Maschinen in Hinblick darauf, wie wahrscheinlich ihr Defekt in der nächsten Zeit ist. Hierzu liest die Predictive-Maintenance-Lösung (PdM) die Daten aus, die von den Sensoren gesammelt wurden und berechnet anhand dieser, ob die Anlage in nächster Zeit einer Wartung oder eines Eingriffs bedarf oder auch ohne Instandhaltung weiterlaufen würde.
Hohe Kosten durch übermäßige Wartung
Die Vorteile liegen auf der Hand: Bei halbjährlichen Intervallwartungen, wie sie Gang und Gäbe sind, werden Maschinen vereinzelt im Zuge eines festen Zeitplans aus der Produktion genommen, um sie zu warten und gegebenenfalls verschlissene Komponenten auszutauschen. Um sicherzustellen, dass eine Anlage nicht ausfällt und somit die gesamte Produktion gefährdet, untersuchen Wartungsteams Maschinen häufiger als nötig.
Dieser „Overservice“ verursacht hohe Ausgaben, indem zum einen die aus dem Betrieb genommenen Maschinen ihre Arbeit nicht verrichten und keinen Umsatz generieren können. Zum anderen ist das Wartungspersonal häufig eingebunden, obwohl es an anderer Stelle vielleicht besser aufgehoben wäre. Auch werden Teile ausgetauscht, die sicherlich noch eine gewisse Zeit funktionieren, aber bis zum nächsten Intervall ausfallen würden.
Darüber hinaus bringt eine Intervallwartung eine Logistik mit, die zusätzlich Kosten verursacht und wertvollen Raum wegnimmt. Wenn für jedes Verschleißteil redundanter Ersatz verfügbar sein soll, muss es ausreichende Lagerkapazitäten für diese Teile geben.
Eine Lösung für Predictive Maintenance kann Kosten, die durch klassische Wartungspraktiken entstehen, erheblich senken. Alle Daten, die Maschinen mit Hilfe ihrer Sensoren generieren, werden an die PdM-Lösung gesendet und von dieser ausgewertet. Das heißt, es werden Profile für die einzelnen Maschinen angelegt, in denen typische Werte für mechanische und thermische Belastungen erfasst sind.
Stellt die Lösung über einen längeren Zeitraum eine Veränderung dieser Werte fest, die abseits der üblichen Schwankungen liegt, berechnet sie anhand dieser, wie lange die Maschine noch funktionieren kann, bis sie aufgrund einer defekten Komponente ausfällt. Alle Ergebnisse werden in einem zentralen Dashboard dargestellt, das auch auf mobilen Endgeräten verfügbar ist.
Einige Lösungen verfügen über ein einfaches Ampelsystem, das die überwachten Maschinen gemäß ihres „Gesundheitszustands“ kategorisiert.
- Geräte, die eines unmittelbaren Eingriffs bedürfen, um weiter funktionieren zu können, erhalten ein rotes Signal.
- Diejenigen, die zwar nicht akut Gefahr laufen, auszufallen, ein Gelbes. Ihre Wartung kann somit geplant werden, was bedeutet, dass Ersatz für die Maschine eingeplant werden kann und Ersatzteile nach Bedarf bestellt werden können.
- Mit einem grünen Licht werden alle Maschinen kategorisiert, die problemlos funktionieren und auch in absehbarer Zeit nicht drohen, auszufallen.
Die Vorteile liegen auf der Hand: Unternehmen können Umsatzeinbußen durch Maschinenausfälle verhindern, indem Defekte bei Geräten erkannt werden, lange bevor sie eintreten. Überflüssige Wartungszyklen werden verhindert, indem sie nur noch bedarfsgerecht durchgeführt werden. Und schließlich werden Wartungsteams innerhalb der Fabrik entlastet, die nur noch ausrücken müssen, wenn eine oder mehrere Komponenten auszufallen drohen.
Herausforderungen bei der Einführung von Predictive Maintenance
Um präzise Ergebnisse liefern zu können, sind mit Sensoren versehene Maschinen und korrekte Daten unabdingbar. Dies stellt viele Unternehmen, besonders in Deutschland, vor Herausforderungen. Viele Fertigungsanlagen weisen ein beträchtliches Alter auf und sind daher nicht mit einer ausreichenden Sensorik oder digitalen Schnittstellen zur Datenverarbeitung ausgerüstet. Die Alternativen sind teuer: Entweder muss eine digitale Sensorik nachgerüstet werden oder der Betrieb muss eine größere Investition tätigen und die Maschinen austauschen, die überwacht werden sollen.
![]()
„Auch wenn eine Maschine mit Sensorik ausgestattet ist, bedarf sie einer regelmäßigen Kontrolle, um kontinuierlich korrekte Daten zu liefern.“
Peter Portner, Senseye
Einige PdM-Lösungen setzen auf künstliche Intelligenz oder lernende Algorithmen, um den Zustand und den Wartungsbedarf von Geräten zu berechnen. Damit die Voraussagen stimmen, muss das Grundmaterial – also die gesammelten Daten – so präzise wie möglich sein.
Laut einer Bitkom-Studie aus dem Jahr 2018 sind bereits 24 Prozent der Maschinen in deutschen Fabriken „smart“, also kommunizieren per Schnittstellen mit anderen Maschinen und Systemen. Im Umkehrschluss bedeutet dies allerdings, dass 76 Prozent über keine vernetzbaren Maschinen verfügen. Somit sind auch Lösungen wie Condition Based Monitoring und Predictive Maintenance hier nicht möglich.
Doch auch wenn eine Maschine mit Sensorik ausgestattet ist, bedarf sie einer regelmäßigen Kontrolle, um kontinuierlich korrekte Daten zu liefern.
Eine weitere Herausforderung können Kosten sein, die die Einführung einer PdM-Lösung mit sich bringt. In einer Bearing-Point-Studie, im Zuge derer 74 hauptsächlich aus dem Bereich Maschinenbau und Automobilindustrie stammende Unternehmen befragt wurden, geben 46 Prozent der Teilnehmer an, dass die hohen Implementierungskosten sie vor Herausforderungen stellten. 61 Prozent sogar sahen den Aufwand, den die Implementierung einer PdM-Lösung mit sich bringt, als größte Herausforderung.
Sobald allerdings eine solche Lösung erst installiert wurde, lassen sich bereits nach kurzer Zeit erste Erfolge nachweisen. Besonders effektive Lösungen liefern bereits 14 Tage nach ihrer Installation Ergebnisse, mit denen die Wartung vorausgeplant werden kann. Je länger die Lösung mit geeigneten Daten versorgt wird, desto präziser werden die Voraussagen.
Fazit
Die Digitalisierung der Industrie nimmt immer weiter an Fahrt auf und Entscheider in Unternehmen haben dies erkannt. Wenn Produktionsbetriebe auch in Zukunft geschäftsfähig bleiben wollen, sollten sie sich mit den Möglichkeiten beschäftigen, die eine Lösung für Predictive Maintenance mit sich bringen kann. Besonders die Kosteneinsparungen nach der erfolgreichen Implementierung sind ein starkes Argument. Interessierte sollten sich vorher informieren, in wie weit ihr Betrieb die notwendigen Voraussetzungen erfüllt, um eine PdM-Lösung einzuführen.
Über den Autor:
Peter Portner ist Managing Director DACH bei Senseye.
Die Autoren sind für den Inhalt und die Richtigkeit ihrer Beiträge selbst verantwortlich. Die dargelegten Meinungen geben die Ansichten der Autoren wieder und entsprechen nicht unbedingt denen von ComputerWeekly.de.