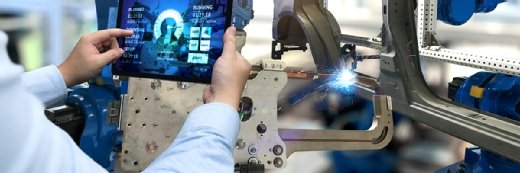
zapp2photo - stock.adobe.com
La IA optimiza la trazabilidad en los flujos de trabajo de manufactura
La industria 4.0 y la internet industrial de las cosas (IIoT) están impulsando la creación y el uso de equipos de visión y sensoriales en la gestión operativa del piso, y el empleo de plataformas híbridas que mejoran el diseño de los flujos de trabajo.
Desde inicios del siglo XX, la preocupación por organizar el trabajo en el piso de producción, con miras a hacer los procesos más eficientes, aún prevalece. Las líneas de producción en masa, con tareas repetitivas y rutinas cíclicas, se fueron perfeccionando a un grado tal que la ética industrial comenzó a concebir mecanismos en los que las personas no estuvieran expuestas a una explotación tan agresiva.
Sin embargo, el temor a que la tecnología de automatización desplace al ser humano sigue latente detrás de los avances industriales y sus cambios económicos.
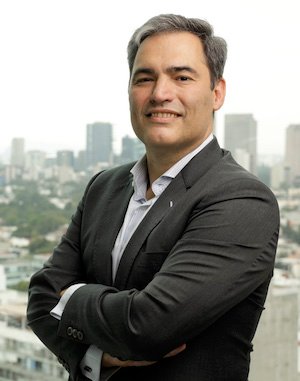
Los tiempos y movimientos en las plantas son aún el centro de atención y cobran fuerza con el arribo de las tecnologías de la información (TI) a la industria de manufactura, al igual que su maridaje con herramientas de deep learning (DL) e inteligencia artificial (IA).
Principios como el análisis cuantitativo del trabajo, la capacitación y la selección correcta del personal para tareas específicas, la alineación de las labores y la interacción entre operadores y el equipo de producción, así como la especialización de las técnicas de producción, se afinarán mejor, recuperando el enfoque humano que actualmente defienden diversas organizaciones.
El desarrollo del ecosistema de producción de la industria 4.0, o de la internet industrial de las cosas (IIoT), conlleva la creación equipos de visión y sensoriales que comienzan a ser aplicados en la gestión operativa del piso. Esta integración está generando plataformas híbridas en las que se combinan la tecnología digital, los sistemas físicos y datos que viajan de un entorno a otro.
Este concepto, desarrollado por Minsait, es conocido como phygital, y en él se consolidan las tres etapas de información y procesos de la operación industrial: gestión, procesos, control e instrumentación. Es en estas tres capas de phygital donde la magia ocurre, y en las que se da sentido a los procesos.
Visibilidad integrada
La aplicación de los componentes de visión en las líneas de ensamble o de manejo de materiales no es nueva, y han sido de gran ayuda para identificar y clasificar material en producción. Se utilizan formas, tamaños, colores, volumen y otros indicadores para asegurar la continuidad, evitar errores y detener posibles riesgos y accidentes para los operadores, entre otras aplicaciones.
Al ser aplicados en el reconocimiento de espacios de trabajo, también se pueden obtener datos relacionados con tiempos y movimientos o perfilar las actividades de los operadores. Los sensores y las cámaras recopilan información de desplazamientos, proximidad, aceleración y orientación. Ya que contienen audio y video, la lectura de tales indicadores nutre las bases de datos de donde se extraen parámetros que pueden ser utilizados posteriormente en sistemas de gestión.
Las actividades registradas pueden advertir de caídas, posturas e incluso la forma de caminar de una persona para identificar cansancio, aburrimiento, desplazamientos o movimientos no adecuados para el tipo de operación que se realiza. Cuando se utilizan en áreas de ergonomía, permiten rediseñar un espacio para mejorar las condiciones de trabajo de un operador, determinar si requiere el apoyo de un colega o un equipo y herramientas, e incluso brindarle capacitación en caso de identificar deficiencias en sus habilidades.
Los sistemas de visión han evolucionado considerablemente a partir de los modelos de identificación corporales y faciales empleados en modelos de IA, los cuales se han desarrollado ampliamente en los vehículos autónomos pues son capaces de detectar gesticulaciones y movimientos que determinen si un conductor está cansado, se distrae demasiado con sus dispositivos móviles o incluso si está divagando. Gracias a que pueden comunicarse con otros sensores del vehículo, los algoritmos de esos sistemas emitirán alertas o tomarán el control del automóvil para evitar accidentes.
Las fábricas hiperconectadas bajo el modelo phygital permiten que estos niveles de integración se consoliden a lo largo de la cadena de suministro, la programación, la manufactura inteligente y la trazabilidad puntual a partir de logística enlazada con sistemas digitales.
Trazabilidad para optimizar la producción
La trazabilidad de las personas y activos, lo que asegura el cumplimiento de la normatividad en la operación para industrias como la aeroespacial, la médica o la automotriz, es de suma importancia.
En una celda de producción, esta información se utilizará en modelos de aprendizaje basados en la tecnología DL para determinar nuevas rutinas de entrenamiento y capacitación, evaluar las habilidades de un operador y reducir así las curvas de aprendizaje. Un programa de entrenamiento puede diseñarse de acuerdo con cada función y tarea, o bien, con cada máquina o dispositivo con el que un individuo vaya a interactuar. Incluso, se podrá determinar el tiempo ideal de una jornada de trabajo con el propósito de mantener la productividad sin afectar la calidad.
Con la utilización de aprendizaje profundo es posible acceder a modelos complejos de datos a partir de sistemas de redes neuronales convolucionales (CNN), que ofrecerán información visual y facilitarán el entendimiento y diseño de nuevos layouts de celdas de trabajo, rutinas y tareas operativas o programas de capacitación.
Ya se han realizado experimentos académicos en torno a ello en actividades de manufactura, en operaciones de mantenimiento y en la producción de automóviles y bicicletas, calculando tiempos de trabajo y mejorando los niveles de calidad en la operación.
El uso de tecnologías de visión y de sensores, en conexión con modelos híbridos (físicos y digitales) y de IA, permitirá establecer esquemas de trazabilidad en los flujos de trabajo, permitiendo incluso partir de procesos de operación virtuales para luego ser utilizados en el mejoramiento de las operaciones fácticas.
Sobre al autor: Guillermo Bilbao es director de Industria de Minsait, una compañía de Indra. Es Ingeniero Industrial por la Escuela Superior de Ingenieros de la Universidad de Navarra y cuenta con un MBA por IESE Business School. Tiene más de 16 años de experiencia en el liderazgo de proyectos estratégicos, finanzas corporativas y análisis de inversiones. Fue director general de PA Consulting en México, donde dirigió proyectos importantes de clientes como Pemex y CFE. Ha trabajado con los principales clientes de la industria de Energía en México.